Are you tired of being the last one to know the latest news in the manufacturing industry? Are you looking for new ways to improve efficiency, accuracy, and safety?
With Augmented Reality (AR) you will never be in the dark again. From the location of your colleagues to malfunctioning machinery, you can get the details with the help of this cutting-edge technology.
That is not all. AR technology offers a unique way to demonstrate industrial equipment, enabling users to interact with the environment in a more practical way. Augmented reality is a great option to help you smoothen your industry process.
The concept of AR may sound like a sci-fi movie, but this is the reality we live in.
Robust growth worldwide
By 2024 there will be an estimated 1.7 billion mobile AR user devices worldwide.
– Statista
In this article, we explore how AR technology can be used to effectively demonstrate industrial equipment, highlighting the potential benefits it offers. We will also look at some examples of how AR is being used to provide a more immersive experience when demonstrating industrial equipment.
By the end of the article, you will have a better understanding of how AR can help streamline industrial processes.
What Role Does Augmented Reality (AR) Play in Manufacturing?
Augmented reality is an interactive technology that combines virtual elements with the physical world to create an immersive environment or experience. It can be enabled through the use of eyeglasses or a simple display piece to enhance the experience for construction workers, plant workers, delivery personnel, and others. The application of this revolutionary technology can mean an extraordinary transformation for industries like Manufacturing and Construction. Equipment maintenance, product demonstration, and much more can be taken to the next level with AR. The possibilities are limitless!
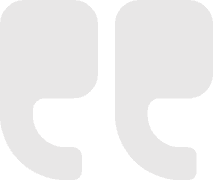
“I believe that augmented reality will be the biggest technological revolution that happens in our lifetimes.”
– Tim Sweeney, CEO and Founder of Epic Games
Hyper-personalized shopping experiences through AR-powered smart malls are revolutionizing retail engagement. By integrating advanced technologies like augmented reality (AR), these malls offer customized interactions to enhance customer satisfaction. AR enables virtual try-on, allowing shoppers to visualize products without physically wearing them. This streamlines the shopping experience and aids in making purchase decisions. Additionally, smart malls provide 3D product visualizations, allowing customers to interact with virtual representations and gain a better understanding of the products. Personalized recommendations based on customer preferences, purchase history, and contextual data further enhance the shopping experience. With AR, smart malls also simplify navigation by providing real-time directions to stores and amenities, saving customers time and effort. Furthermore, interactive advertising using AR engages customers by allowing them to scan QR codes or markers for additional information and promotions. Overall, AR-powered smart malls bridge the gap between online and physical shopping, offering customers personalized experiences, convenient virtual try-ons, and enhanced product visualization.
Challenges in The Manufacturing Industry Today
The manufacturing and equipment demonstration industry is facing a number of challenges in today’s market. With increasing global competition, rising costs, and surging demand for quality products, the industry is being pushed to its limit in order to stay competitive. To make matters worse, the industry is also facing a skill gap with the lack of qualified workers.
Unplanned downtime in manufacturing can lead to significant losses in productivity, resulting in delays customer dissatisfaction, and reduced revenue.
Did You Know
Research shows that unplanned downtime costs an estimated $50 billion each year.
– Wall Street Journal.
Such downtime can interrupt the entire production line, causing major issues with meeting customer demands, managing schedules, and meeting deadlines. In addition, unplanned downtime can lead to decreased morale among employees and an overall decrease in efficiency.
Did You Know
Studies revealed that a three-year average showed that 82% of companies experienced at least one unplanned downtime outage.
– BusinessWire
Here are some specific challenges faced by the manufacturing industry:
Struggle to anticipate future demand today
Most businesses struggle to choose the right forecasting approach despite substantial advancements in demand forecasting and information technology. A major challenge is the lack of effective monitoring systems that would enable them to forecast effectively helping them decide how many goods they should sell in the next few months. This can result in disappointed clients and plummeting sales.
Skilled labor Deficiency syndrome
The manufacturing industry is facing a severe crisis due to the looming retirement of the baby boomer generation, causing what we call skilled labor deficiency syndrome or shortage of skilled labor. Automation and robotics can help reduce the labor gap, but humans will still be required to assess, solve problems, and manage the machinery. This labor gap is one of the most pressing issues for the manufacturing industry today. Employers must take steps to address this problem to ensure the long-term stability of their businesses.
Managing inventory
Managing inventory is still a challenge for the manufacturing industry, but automation is improving things. Still, many manufacturers manage their inventories manually. Inventory management can be simplified by using the software. Manual stock checks result in mistakes, shortages, excess, and unidentified losses. There is a lot of pressure on businesses to deliver high-quality goods consistently. On the other hand, if a manufacturer has trouble keeping track of inventory, shortages, and other problems could arise.
Identifying, managing, and evaluating sales leads
Manufacturing companies find it challenging to identify potential leads. This results in a glorified search for unpromising opportunities and missing out on high-potential leads. Another problem that manufacturing companies experience is not being able to keep track of sales leads. Each sale lead is unique in terms of persona, preferences, and requirements. Hence, they must be treated individually.
The question is: how can manufacturing overcome these challenges successfully? Let’s see.
Augmented Reality - The Ultimate Solution to Manufacturing Challenges
The Good News – AR has become a powerful tool for manufacturers and maintenance and demonstration technicians, providing them with the ability to easily access and visualize complex data in real time. AR is also being used to create virtual training simulations without the need for costly physical training. A recent study shows that manufacturers around the world are recognizing the impact of AR.
Did You Know
“The global augmented reality & virtual reality in manufacturing market size was valued at USD 5.57 billion in 2021 and is expected to expand at a compound annual growth rate (CAGR) of 29.3% from 2022 to 2030.”
– Grand View Research
AR gives manufacturers the ability to monitor production processes from afar and troubleshoot problems faster and more efficiently. Additionally, AR can be used to create interactive demonstrations of products and services, allowing manufacturers to better showcase their capabilities to potential customers.
An example of this is the launch of the mixed reality headset HoloLens 2 by Microsoft Corporation Inc.
Consider the impact of Microsoft Hololens 2:
- Manufacturers saved an average of $3,500 per avoided expert trip.
- Manufacturers increased revenue by up to 5% with mixed reality.
- Manufacturers reduced training time by 75% at an average savings of $30 per labor hour.
– Forrester Research
How Can AR be Leveraged in The Best Way?
AR technology can disrupt businesses in many ways. For example, in manufacturing, workers can use AR wearables to measure changes, identify unsafe working conditions, or visualize a finished structure or product. The beauty of it is that you can use it to overlay text, stats, and information relevant to the worker’s current task.
Robust growth worldwide
Global AR glasses market is expected to reach 8.8 million units by 2026.
– CISION PR Newswire.
The question is how you can make this work for your business. Here are a few ways:
Training new personnel does not have to be a burden anymore! Thanks to AR application, new workers can now be informed and protected with minimal effort and additional resources. An enterprise-centric AR application can provide step-by-step guidance, contextual documentation and manuals, additional resources, and even barcode scanning if required.
AR is revolutionizing warehouses and making it easier for workers to do their job. With AR, workers can quickly access information on where goods are located and scan necessary data to process orders. This eliminates the need to spend time manually searching for items.
AR can equip maintenance crews with all the information they need – from the exact equipment and hardware that requires servicing to the date of the last services, and even potential points of failure.
Rather than manually searching for potential issues, AR devices can give workers real-time updates on their visits to any factory or warehouse. This makes it easier to identify and repair equipment quickly, allowing them to respond faster and more accurately.
AR can enable executives and directors to view the product being developed in real-time. This enables them to provide valuable input and direction without having to go back and forth.
Promising future: PWC researchers predict that the integration of VR and AR into product and service development could raise GDP by a total of $359.4 billion by the year 2030.
Personnel can detect and monitor assets in real-time using AR, which leads to more accurate and faster identification. Furthermore, they are able to access associated digital data, such as the equipment’s maintenance history and spare parts, to ensure a quick repair or replacement.
Additionally, AR can provide the output of current equipment indicators, like machine temperatures, humidity levels, and pressure settings, by connecting a series of sensors to an AR headset. For example, these sensors can monitor a factory’s HVAC system. The feedback it could provide on temperatures and humidity levels would help to keep the production facility’s working conditions at the optimal level.
From smartphones to airplanes, every product needs to be assembled precisely. Product design and development help ensure assembly instructions are followed. Product design and development involves creating a detailed blueprint of a product, outlining the components and how they fit together. This serves as a guide for putting together complex assemblies. AR technology eases this task ensuring there is no room for error.
AR has revolutionized spatial computing, allowing us to visualize data in the physical world and create interactive experiences with physical objects. In the manufacturing industry, it has streamlined processes by providing a way to view extra data and context around the items being worked on.
For instance, producers can use AR to gain insights about a particular material such as its density, hardness, or other characteristics in 3D space with the help of a headset like an Oculus or HoloLens. Additionally, AR makes it possible to preview the finished product and any issues that may arise during production.
Did you know? As reported by Grand View Research, the growth of Augmented Reality in the manufacturing sector has been significant, with the global manufacturing market estimated to be valued at USD 5.6 billion in 2021. This market is projected to increase at a CAGR of around 30% from 2021 to 2030.
Augmented Reality services provides customers with the ability to virtually connect with a trained technician who can view their environment in AR and give them instant help. This could range from offering easy directions to assisting with intricate processes. Suppose a customer has an issue with their device. In this case, an expert can use AR to give step-by-step instructions and even view the customer’s environment on a video call.
Robust growth worldwide: By 2030, the AR smart glasses market is estimated to reach USD 97,384.1 million, at a CAGR of 20.3% during the forecast period 2023 to 2030. – CDI.
Did You Know
By the year 2025, the total market value of Industrial Augmented Reality is projected to reach US$70 Billion.
– PR Newswire.
Use Cases - Top Industries That Understand ‘Seeing Is Believing!’
Manufacturers across multiple industries globally have embraced AR technology, recognizing its potential to overcome various challenges and deliver increased value.
Please take a look at four leading manufacturing industries that are leveraging the power of AR to boost their operational efficiency.
Did You Know
The AR & VR market is currently producing an annual estimate of $25.21 billion, and is estimated to see exponential growth at a CAGR of 15.6% through 2027.
– Statista.
Electronics manufacturing
In the electronics manufacturing sector, both output quantity and product quality are essential for a successful business. Although it is big brand names that we see on laptops and phones, the actual manufacturing is often completed by contracted companies. These companies need to ensure that their margins of error remain low (as low as 1-2%) to meet the needs of their clients.
To do this, contractors need to employ workers that are capable of learning quickly and working without errors. However, only a few are able to meet the expected standard due to high turnover rates in the industry.
To add to that, the electronic industry is innovating every other minute. We can only imagine how often work instructions have to be updated throughout the same time frame. AR-guided instructions have been a boon here as they help visualize those work instructions making them faster and easier to comprehend.
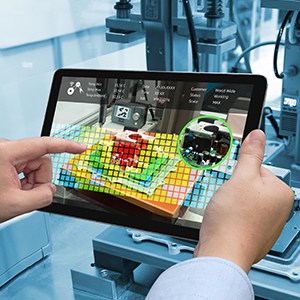
Automotive industry
It is an understatement to say that production possibilities for automotive manufacturing are vast. For example, Ford has 41 different models around the world, not to mention the variations of those models, with some having up to 15 different styles.
Considering the different colors and the potential for individual customizations, it’s clear that production could do with some help. With the help of augmented reality, OEMs and tiered suppliers can quickly and accurately transition from one model to the next, such as going from the Ford Ranger to the Mustang in a single hour.
Did You Know
According to Statista, AR in vehicles is expected to reach an economic value of $2 billion to $3 billion by 2025. And it is expected to grow to between $4 and $7 billion by 2030.
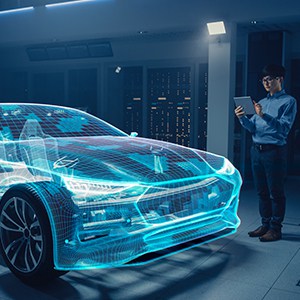
Use Cases:
AR can be particularly useful for the assembly of headliners, one of the largest parts of the manufacturing process. In order to precisely place padding, glue, wire harness, and other components, workers must have accurate positioning information, to match the model they’re working on. With AR-enabled digital work instructions, workers can have an exact visual template of what needs to be produced, with placements mapped out onto the part in millimeter precision. By using AR technology, automotive manufacturers can ensure an efficient, accurate assembly process.
Medical manufacturing
Did You Know
According to Statista, AR in hospitals is expected to reach an economic value of $20 billion to $30 billion by 2025. And it is expected to grow to between $40 and $90 billion by 2030.
Medical and pharmaceutical manufacturers must adhere to stringent protocols and testing methods to gain FDA approval. Maintaining the utmost integrity is of paramount importance in order to ensure safety both for the operator and end-user. This is crucial irrespective of the nature of the process – be it kitting, pill counting, or drug development.
Augmented Reality verification is becoming commonplace among medical manufacturers. AR can act as a guide for workers, helping them identify from which bin to pick the component, what tool to use, and where to place it correctly. To confirm that the product is properly assembled, product validation can be achieved through the use of high-precision machine vision cameras and sensor technology, right down to the last bolt or screw.
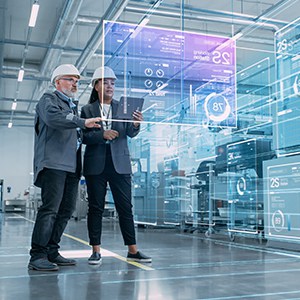
Aerospace and defense
When it comes to aerospace and defense, quality is of the utmost importance. Products must be built and assembled with 100% accuracy and precision, even if it means sacrificing throughput. As a passenger, you would be much more willing to board a plane knowing it had been properly assembled with no missing parts.
To achieve higher levels of quality, aerospace and defense companies often rely on a single-piece flow process. This process involves sub-assemblies being built and moved from station to station until the final product is completed. With augmented reality work instructions, operators can be guided through the entire production process.
This technology can effectively reduce errors and increase throughput. Single-piece flow is particularly advantageous for aerospace and defense due to the high variation and long production cycle times. This process helps to ensure products are built correctly, which is critical for safety and reliability.
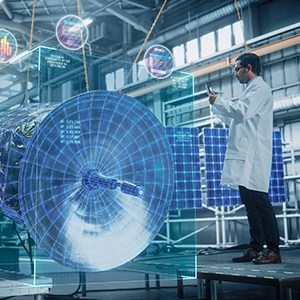
Did You Know
By the year 2025, the total market value of Industrial Augmented Reality is projected to reach US$70 Billion.
– PR Newswire.
There are many more applications of Augmented Reality in Manufacturing that can be used effectively to increase efficiency, eliminate defects, visualize products and more. In this video, you can see some use cases which include industrial product demos, marketing demos, gamified experience of products, defect detection visualizer, and more.
Top Benefits of Utilizing AR In Manufacturing and Equipment Maintenance & Demonstration
Augmented reality (AR) is revolutionizing the way industrial equipment is maintained and demonstrated. By overlaying digital information onto the physical world, it provides intuitive and efficient ways of training and repairing industrial equipment. Here are the top benefits of utilizing AR in manufacturing and equipment maintenance & demonstration:·
- Improved training and maintenance efficiency: AR allows workers to more easily access instructions and receive real-time feedback from a remote expert. This reduces the need for costly and time-consuming on-site visits.
- Streamlined production cycles: AR industrial applications can give shop floor personnel limitless and contextualized support in real time. This can streamline production cycles and instantly alert workers of any mistakes, allowing them to take care of any potential issues before they impact efficiency or quality. Moreover, these apps provide workers with a visualization of the final product before its creation, so they can comprehend how their individual task is relevant to the bigger picture.
- Cost savings: AR-based training and maintenance reduce the cost of parts and labor, while also eliminating the need for expensive specialized tools and equipment.
- Time-saving: AR can drastically reduce the time spent on maintenance in a manufacturing setting. Operators, technicians, and engineers have the benefit of obtaining live assistance with the maintenance process, while experienced professionals can provide remote help to complete tasks as quickly as possible. This access to added resources minimizes downtime and maintenance and allows for a higher-quality outcome and faster delivery times. Plus, AR systems can recognize mechanical issues and propose solutions to prevent further complications.
- Promotes informed decision-making: Augmented Reality grants manufacturing workers a comprehensive overview of various data points at a glance, allowing them to make more informed decisions. This is achieved by rendering the data into a visual format, enabling the discovery of trends that may otherwise be overlooked. Additionally, it provides contextual data such as instructions on how to use a machine or performance metrics. All of this serves to streamline data access while facilitating the resolution of problems and the optimization of processes.
- Enhanced customer experience: AR-powered equipment demonstrations can provide customers with a realistic, interactive experience, allowing them to better understand how the equipment works.
Did You Know
Luxury brand Gucci made news for selling a bee-embroidered Gucci Dionysus bag in the game for $4,115 on a game Roblox that is almost $800 USD more than the real Dionysus bag that sells for $3,400.
– TFL
Overall, augmented reality is proving to be a powerful tool for the training of workers and maintenance of industrial equipment. AR has become an invaluable tool for manufacturers, allowing them to virtually repair and construct equipment, conduct demonstrations, and maintain equipment.
Using AR, technicians can utilize a headset to visualize and interact with equipment in an interactive 3D environment. This opens up the possibility for virtual repairs, allowing technicians to see what needs to be fixed without the need to physically dismantle the equipment.
AR also provides a new level of interactivity during the equipment demonstration process. With AR, customers are able to visualize and explore the equipment in a way that was never before possible. This can help increase customer engagement and understanding of the equipment.
Finally, AR can help with the maintenance process, allowing technicians to gain a better understanding of the equipment and detect any problems before they even arise.
The integration of the Industrial Internet of Things (IIoT), augmented reality (AR), and big data is transforming equipment maintenance. With IIoT, industrial equipment is connected to sensors that collect real-time data for monitoring and predictive analytics. AR enhances maintenance procedures by providing technicians with real-time data visualizations, step-by-step instructions, and remote expert support. Meanwhile, big data analytics processes large volumes of data from sensors, maintenance logs, and historical records to identify patterns and predict equipment failures. By combining these technologies, equipment maintenance shifts from reactive to proactive, minimizing downtime, optimizing performance, and reducing costs. Real-time data monitoring, augmented visualization, and predictive maintenance empower technicians to diagnose and repair equipment more efficiently. Additionally, remote collaboration capabilities improve communication and enable expert guidance regardless of physical location. Overall, the integration of IIoT, AR, and big data brings new dimensions to equipment maintenance, enhancing productivity, efficiency, and reliability in industrial operations.
The Difference between AR and VR
Augmented Reality is the use of technology to combine the digital and physical worlds to create an enhanced user experience. Visual, audio and sensory digital elements are used to create this experience in the real world.
Virtual Reality, as its name signifies, is the use of technology to create an exclusively virtual world. Using a head-mounted display (HMD), users can enter a simulated 3D environment as virtual beings.
Though they are sometimes used synonymously and have both made a great impact on technology and business as we know it, AR and VR are in fact two separate technologies. Here we see a few differences between the two.

Augmented Reality
- AR uses elements of the digital world but brings them into a real world setting.
- AR does not require a headset.
- AR can be applied to elements in the real world as well the virtual realm.
- An AR user is able to control his presence in the real world.

Virtual Reality
- This is a completely simulated experience, set in the virtual world.
- You will need a headset to use VR
- VR can only be applied to virtual settings and cannot enhance real world elements.
- VR takes complete control of the uses in the virtual world.
Debunking A Few Myths About Implementing AR
Augmented Reality (AR) is being embraced by many industries as a game-changer for training and maintenance activities. However, there are many misconceptions and myths circulating around AR implementation in the field of industrial equipment maintenance and demonstration.
Myth #1: Implementing AR is a costly affair.
This misconception has caused companies to fear that it is very expensive in terms of hardware and software. However, the truth is that AR can be very cost-effective since it is easy to install and maintain, and the hardware and software costs are quite reasonable.
Myth #2: AR would require a lot of training and technical expertise.
This is not the case. AR tools are designed to be intuitive and user-friendly, allowing users to quickly and easily learn how to use them.
Myth #3: Implementing AR is difficult and time-consuming.
In actuality, the installation and implementation of AR for maintenance and demonstration are relatively quick and straightforward. Talk to one of our experts who will run you through how simple this can be!
Strategizing Successful AR Implementation with Fingent
AR has great potential to revolutionize the way we do business. However, successful implementation can be tricky. It is important to have a clear strategy for how to use the technology in order to maximize its value and avoid any possible pitfalls.
One key step is to identify any existing gaps in your current process and consider how AR could help fill those gaps. Additionally, invest the necessary resources in the development of AR solutions to ensure that the technology works as intended. Finally, ensure that all stakeholders are on board with the AR implementation and that they are aware of its potential benefits.
Fingent is a custom software development company with expertise in developing budget-friendly, yet innovative AR solutions. We have the perfect solution for your challenges. Our custom AR apps are designed to give you the edge you need. Our team of experts will work with you to help you maximize your business growth and success. Do not wait to get ahead of the pack – contact Fingent today to know more.