How CxO’s can Leverage IoT to Transform Field Service Operations
Think of field service operations, and the odds are of the term being associated with inefficiency, delays, and other ills. Field service operations are not just reactive in nature, but characteristically prone to high incidence of human error, induced by various causes such as skill deficiency of the technician, lack of adequate tools or information, technical limitations, inconsistency or ambiguity of instructions, time limitations, and so on.
There is a solution in sight though. The IoT revolution offers a chance to not just set things right, but also to transform the ecosystem itself in a big way.
1. Optimize Provisioning of Resources
M2M, the core subset of IoT, enable sensors on devices or “things” to communicate with one another, transmitting location, movement, temperature, environment, and other relevant data. Top service teams of today tap into M2M data to gain visibility into the device they maintain, and offer timely support.
Sparked, a Dutch start-up, places such M2M enabled wireless sensors on cattle, to alert farmers when a cow is sick, pregnant, or in some other state. Replicating the same set-up to devices allow field service technicians to detect anomalies in real-time. The service controller taps into the technician’s geolocation, and assigns the repair job to the best poised technician closest to the location.
2. Undertake Proactive Preventive Maintenance
Very often the agony users express on finding a device conked out, is not concerns about what happened to the device, but the downtime. The fix itself may be simple and even obvious, but the wait can be nerve wrecking. Service firms may use IoT to change over from a reactive service model, waiting for the customer to call and log a service request, to a proactive model that automatically predicts problems, and thereby play into the pressing need of instant gratification.
Consider the case of Diebold, the Ohio-based international ATM manufacturer, responsible for the maintenance of repair of thousands of ATMs spread across the globe. Its global service team leverages M2M generated data to identify how long a specific component has been in use, and how many times a machine has been used. The team keeps track of data emitted by each ATM, on a 24×7 basis, to identify when a technician need to replace a specific machine’s parts, and schedules services accordingly, on a proactive basis, pre-empting machine failure.
An Intelligent Business Operations Platform that embeds actionable predictive analytics into business processes equips field technicians with insights not available before. It empowers them to take data-driven decisions, allowing them to fix things before they break. Aberdeen Group estimates 50% of top-performing service companies having such preventive maintenance models in place, with 26% of them able to resolve issues remotely, even without making site visits.
3. Invest in Remote Diagnostics
IoT-enabled remote diagnostics help to cut downtime even further.
The trends and patterns made explicit by M2M data allow technicians to pin-point what is wrong, which components to replace, which tools to carry to the site, and more. This enables more first-time fixes, reducing downtime for the customer and greatly reducing rolling inventory for the service provider.
In many cases, such as, if the equipment simply requires reset; the task may be done remotely, by issuing commands to the sensor, eliminating the need for a site visit entirely. Medical tech provider Welch Allyn’s cloud-based M2M solution that runs software updates and even makes remote repairs to their equipment from afar is a good case-in-point.
Beecham Research estimates such remote monitoring and diagnostics reducing service visits by as much as 60%. Diebold could resolve about 17% of their issues remotely without ever sending a technician onsite. Needless to say, the reduced downtime improves customer satisfaction greatly.
4. Empower Field Technicians to Ensure Better Fixes
IoT-powered wearables offer the potential of making field service technicians much more potent and effective. He could, for instance, tap onto the NFC tag attached to the device being repaired, and read notes on previous maintenance carried out. Taking cues from surgeons using Google Glasses, less experienced field technicians could have ready access to their instruction manuals, or hook up with other experts to get insights and instructions on complex problems, sparing additional field visits.
Taking the concept to the next stage, IoT and wearable technology offers the potential of self-service and eliminate the need for service technicians to visit the site at all. A smart glass endowed user could get accurate step-by-step instructions to fix the device, from a remote technician who draws in M2M data from the device being fixed.
5. Develop Better Business Models
Applying M2M and the larger IoT technology improves the efficiency of the field service team manifold, and help them do more with lesser resources. It helps to propel FSM 2.0, which promises a win-win proposition, with the provider able to adopt outcome-based revenue models, and pass on some of the gains of improved productivity and efficiency to customers. The service team may also share M2M intelligence with the customers, especially at the invoicing phase, forging an effective working relationship and improving transparency of the whole exercise.
IoT promises a better, transformed world, where field service operations never had it so good. But it still requires effective solutions to tap into the possibilities. ReachOut Suite, for instance, offers a complete solution for all your field service requirements, allowing you to manage everything seamlessly, from one central console.
Stay up to date on what's new
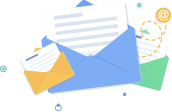
Recommended Posts
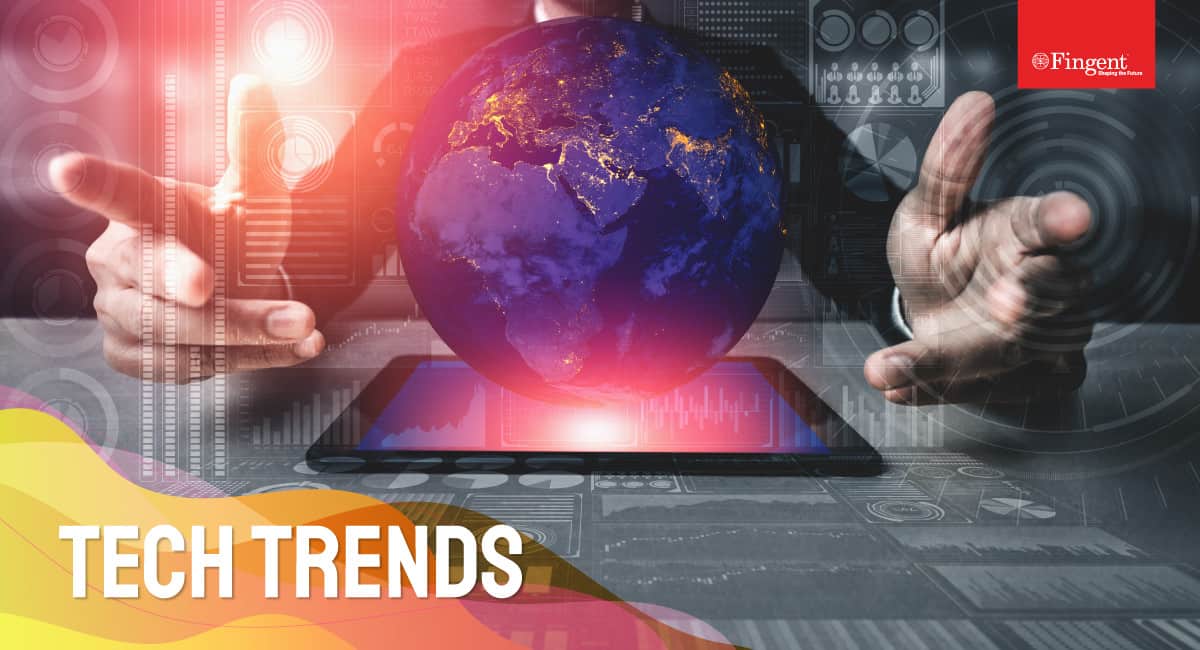
28 Oct 2020
11 Tech Trends That Will Disrupt Businesses in The Next 2 Years
Supercharge Your Business with These 11 Hot Tech Trends Technology is having an ever-greater impact on our personal lives and most importantly on the way we do business. The business……
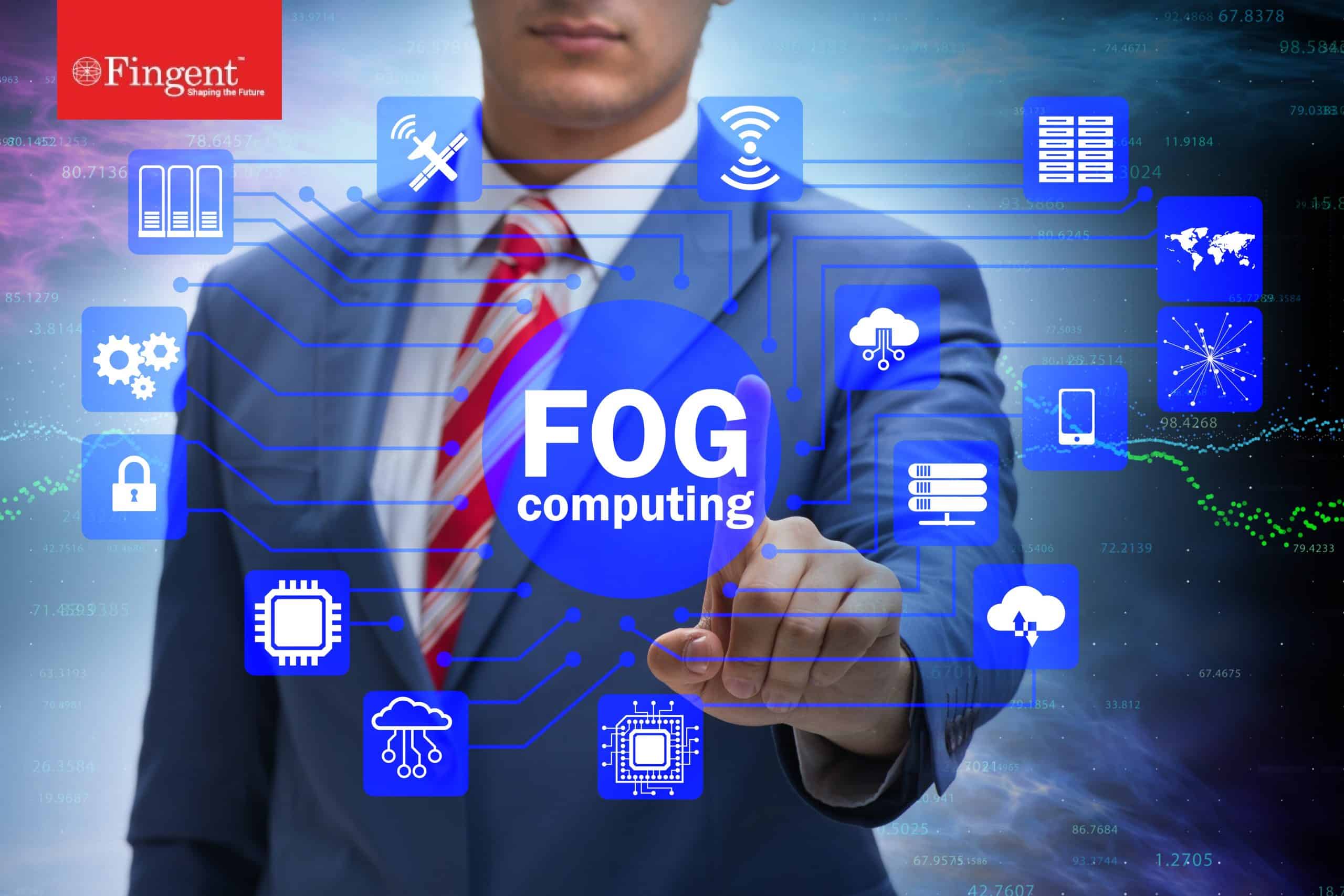
25 Jun 2020
What Is Fog Computing and How Does It Work?
How Can Your Business Benefit from Fog Computing? How much data do we create every day? The World Economic Forum reports that the entire digital world is expected to reach……
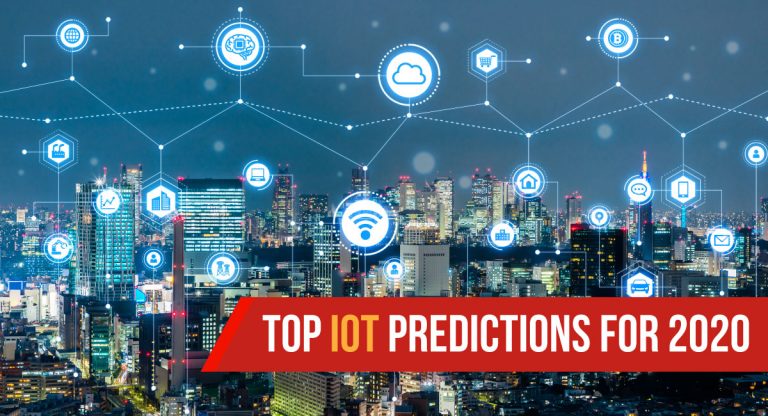
02 Mar 2020
Gearing up for IoT in 2020
How to prepare for IoT in 2020? It’s 2020 already and the Internet of Things (IoT) is here to stay. We’re at the cusp of a new era wherein intelligent digital……
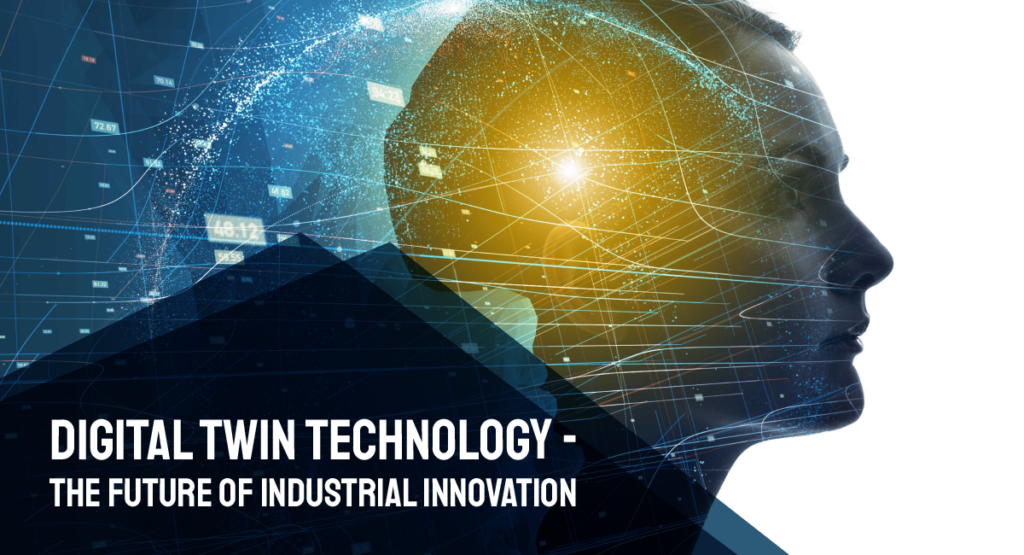
12 Jul 2019 Manufacturing Healthcare
Digital Twin Technology Reshaping IoT-Enabled Environments
Evolution Of The Digital Twin Technology What is a digital twin? Digital Twins can be best defined as digital copies or virtual replicas of physical assets. Data scientists can make use……
Featured Blogs
Stay up to date on
what's new
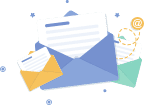
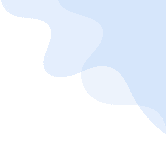
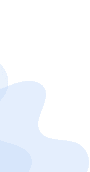